PENERAPAN LEAN SIGMA UNTUK ELIMINASI WASTE PADA PROSES PRODUKSI UPPER SANDAL DI PT XYZ, SIDOARJO
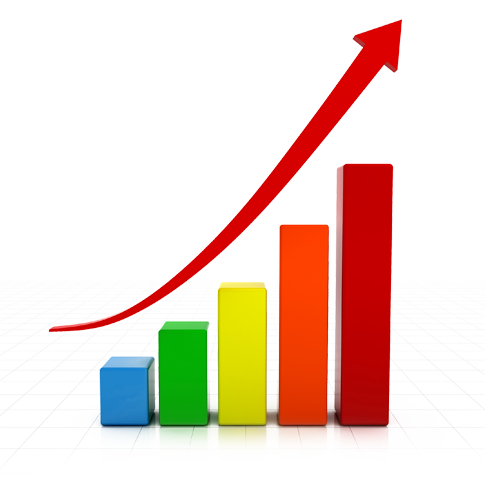

Abstract
Abstract— PT XYZ is a manufacturing company that produces sandals and component sandals with distribution area for the entire region of Indonesia. The type of product that is most often produced by the company is the sandal component, more specifically is the upper sandal product. In the initial observations found several problems related to waste in the upper sandal production process. The purpose of this research is to identify waste that occurs in the company and provide improvement solution to minimize it. The research method used is Lean Sigma method with DMAIC stages (Define, Measure, Analyze, Improve and Control), the Lean method used is Waste Assessment Model (WAM). In the define stage, the research object will be determined, CTQ identification and production process flowchart will be made. At the measure stage, will be done calculate the process capability and identify critical waste in the company using WAM method, this method is divided into 3 parts, the seven waste relationships, the Waste Relationship Matrix (WRM) and the Waste Assessment Questionnaire (WAQ). In the analyze stage, an analysis of the WAM results will be done using the 5 whys analysis method, hazard analysis table and Failure Mode and Effect Analysis (FMEA). In the improve stage will be done the design of improvement solutions for several waste problems that have a high level of hazard and a high level of risk, based on the results of the analyze stage. At the control stage, the control design will be created for improvement solutions that implemented in the company. Based on the results of this research, it was found that the critical waste in the company was waste defect (32.24%), waste transportation (28.23%) and waste overprocessing (25.47%) and there were 25 design improvement solutions with 5 improvement solutions that were feasible to be implemented in company.
Keywords: upper sandal, lean sigma, WAM, 5 whys, hazard analysis table, FMEA
Abstrak— PT XYZ merupakan perusahaan manufaktur yang memproduksi sandal dan komponen sandal dengan wilayah distribusi untuk seluruh wilayah Indonesia. Jenis produk yang paling sering diproduksi oleh perusahaan adalah komponen sandal yaitu produk upper sandal. Pada pengamatan awal ditemukan beberapa masalah yang berkaitan dengan waste pada proses produksi upper sandal. Tujuan dari penelitian ini adalah mengidentifikasi waste yang terjadi di perusahaan serta memberikan rancangan solusi perbaikan untuk meminimasinya. Metode penelitian yang digunakan adalah metode Lean Sigma dengan tahapan DMAIC (Define, Measure, Analyze, Improve dan Control), metode Lean yang digunakan adalah Waste Assessment Model (WAM). Pada tahap define akan dilakukan penentuan objek penelitian, identifikasi CTQ dan pembuatan flowchart proses produksi. Pada tahap measure akan melakukan perhitungan kapabilitas proses dan mengidentifikasi waste kritis pada perusahaan dengan menggunakan metode WAM, metode ini yang dibagi menjadi 3 bagian yaitu seven waste relationship, Waste Relationship Matrix (WRM) dan Waste Assessment Questionnaire (WAQ). Pada tahap analyze akan melakukan analisis dari hasil WAM dengan menggunakan metode 5 whys analysis, tabel analisis bahaya dan Failure Mode and Effect Analysis (FMEA). Pada tahap improve akan membuat rancangan solusi perbaikan untuk beberapa permasalahan waste yang memiliki tingkat bahaya dan tingkat resiko tinggi berdasarkan hasil dari tahap analyze. Pada tahap control akan membuat design rancangan control untuk solusi perbaikan yang diimplementasikan di perusahaan. Berdasarkan hasil penelitian, didapatkan waste kritis pada perusahaan adalah waste defect (32,24%), waste transportation (28,23%) dan waste overprocessing (25,47%) dan terdapat 25 rancangan solusi perbaikan dengan 5 solusi perbaikian yang feasible untuk diimplementasikan di perusahaan.
Kata kunci: upper sandal, lean sigma, WAM, 5 whys, tabel analisis bahaya, FMEA
Downloads
References
Annisa, N. (2014). Pendekatan Lean Six Sigma Untuk Mengurangi Waste Proses Produksi Brown Paper (Studi Kasus: PT Kertas Leces, Kabupaten Probolinggo) (Doctoral dissertation, Universitas Brawijaya).
Anthony, J., & Kumar, M. (2011). Lean sigma: Research and Practice. s.l.:Ventus Publishing Aps.
Cudney, E. A., Furtere, S.L., & Dietriech, D.M. (2014). Lean Systems: Applications ans case Studies in Manufacturing, Service, and Healthcare. Boca Raton: CRC Press
Daonil, K. (2012). Implementasi Lean Manufacturing Untuk Eliminasi Waste pada Lini Produksi Machining Cast Wheel dengan Menggunakan Metode WAM dan VALSAT, Depok: Universitas Indonesia.
Dumitrescu, C., & Dumitrache, M. (2011). The Impact of Lean Six Sigma on the Overall Results of Companies, Volume 14, pp. 535-544
Gaspersz, V. (2007). Lean Six Sigma for Manufacturing and Service Industries, Jakarta: PT. Gramedia Pustaka Utama.
George, M. J. (2003). Resolving the mysteries of six sigma: Statistical Construct and Engineering Rationale. Scottsdale: Scottsdale.
Hines & Rich. et al. (1997). The Seven Value Stream Mapping Tools. International Journal of Operations & Production Management, 17 (1), pp. 46-64
Magar, V. M., and Shinde, V. B. (2014), “Application of 7 Quality Control (7 QC) Tools for Continuous Improvement of Manufacturing Processes”. International Journal of Engineering Research and General Science, 2(4), pp. 364-371
Morgan, J., & Brenig-Jones, M. (2012). Lean sigma for Dummies. Chichester: John Wiley & Sons, Ltd.
Rawabdeh, I. A. (2005). A model for the assessment of waste innjob shop environments. Emerald Insight. 25(8), pp. 800-832
Ristyowati, T., Muhsin, A., and Nurani, P. P. (2017). Minimasi Waste Pada Aktivitas Proses Produksi Dengan Konsep Lean Manufacturing (Studi Kasus di PT. Sport Glove Indonesia). Opsi, 10(1), pp.85-96.
Sayer, N. J., & William, B. (2007). Lean for Dummies. Canada: Wiley Publishing, Inc
Sugimori, Y., Kusunoki, K., Cho, F., and UCHIKAWA, S. (1977). Toyota Production System and Kanban System Materialization of Just-In-Time and Respect-for-Human System. The international journal of production research, 15(6), pp.553-564.

This work is licensed under a Creative Commons Attribution-ShareAlike 4.0 International License.
- Articles published in CALYPTRA are licensed under a Creative Commons Attribution-ShareAlike 4.0 International license. You are free to copy, transform, or redistribute articles for any lawful purpose in any medium, provided you give appropriate credit to the original author(s) and the journal, link to the license, indicate if changes were made, and redistribute any derivative work under the same license.
- Copyright on articles is retained by the respective author(s), without restrictions. A non-exclusive license is granted to CALYPTRA to publish the article and identify itself as its original publisher, along with the commercial right to include the article in a hardcopy issue for sale to libraries and individuals.
- By publishing in CALYPTRA, authors grant any third party the right to use their article to the extent provided by the Creative Commons Attribution-ShareAlike 4.0 International license.