REDUCING MANUFACTURING LEAD TIME AND WASTES IN RIDEON CARS PRODUCTION LINE IN PT. XYZ THROUGH VALUE STREAM MAPPING IMPLEMENTATION
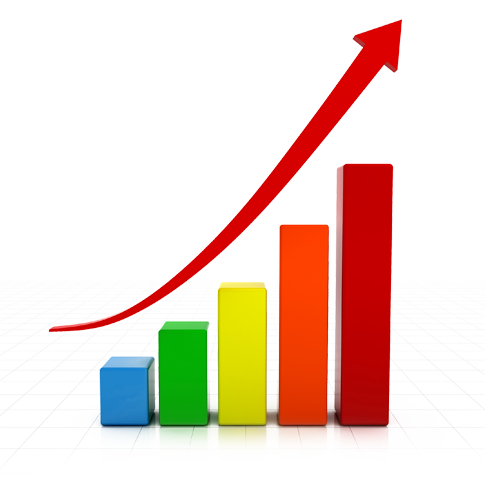

Abstract
Abstract -- This research is empirically designed to implement Value Stream Mapping to PT. XYZ’s ride-on cars production line as well as showing effectiveness of Value Stream Mapping to manufacturing lead time and wastes reduction. This research examines rideon cars production process in PT. XYZ where data were obtained mainly from direct observation in January 2018 and some from plant’s data. Former data showed fluctuation in manufacturing lead time. Furthermore, only one out of seven wastes was firstly detected by production team which was defect rate shown in November and December 2017 data. Value Stream Mapping is one of lean manufacturing tools used to reduce wastes which also leads to manufacturing lead time reduction. The result of this research finds that Value Stream Mapping is efficient in identifying wastes of motion, transportation, and waiting as well as reducing most of wastes after implementation in PT. XYZ is done and finally impacted on manufacturing lead time reduction.
Keywords: Lean Manufacturing, Flow Process Chart, Process Activity, Value Stream Mapping, Wastes, Manufacturing Lead Time
Downloads
References
Council of Supply Chain Management Professionals. (2016). CSCMP Supply Chain Management Definitions and Glossary. Retrieved 11 13, 2017, from Council of Supply Chain Management Professionals: http://cscmp.org/CSCMP/Educate/SCM_Definitions_and_Glossary_of_Terms/CSCMP/Educate/SCM_Definitions_and_Glossary_of_Terms.aspx?hkey=60879588-f65f-4ab5-8c4b-6878815ef921
Dave, Y., & Sohani, N. (2012). Single Minute Exchange of Dies: Literature Review. International Journal of Lean Thinking, 3(2), 27-38.
ECSLAB. (2008, 9). Measuring Moisture of Plastic Pellets. Retrieved from ECSLABONLINE: http://www.ecslabonline.com/pdf/mettler-toledo-plastik-aplikasyonu.pdf
Ferradas, P. G., & Salonitis, K. (2013). Improving Changeover Time: A Tailored SMED Approach for Welding Cells. Forty Sixth CIRP Conference on Manufacturing Systems (pp. 598-604). United Kingdom: Cranfield University.
Gavali, R., Chavan, S., & Dongre, G. D. (2016). Set-up Time Reduction of a Manufacturing Line using SMED Technique. International Research Journal of Engineering and Technology (IRJET), 3(7), 1748-1750.
Groover, M. P. (2007). Work Systems: The Methods, Measurement and Management of Work (1sted.). England: Pearson Education Limited.
Hartanti, L. P. (2016). Work Measurement Approach to Determine Standard Time in Assembly Line. Proceedings of 31st IASTEM International Conference (pp. 49-52). Pattaya: ISBN.
Hopp, W. J., & Spearman, M. L. (2004). To Pull or Not to Pull: What Is the Question? Manufacturing & Service Operations Management, 6(2), 133-148.
Institute of Industrial & Systems Engineers. (1982). Time and Motion Study. Retrieved from Institute of Industrial & Systems Engineers: http://www.iise.org/details.aspx?id=645
Karmarkar, U. S. (1993). Manufacturing Lead Times, Order Release and Capacity Loading. In S.C. Graves, Handbooks in OR & MS (Vol. 4, pp. 287-328). Rochester, New York: Elsevier Science Publishers.
Karsten, L. (1996). Writing and the Advent of Scientific Management: The Case of Time and Motion Studies. Scandinavian Journal of Management, 12(1), 41-55.
Kementrian Perindustrian Republik Indonesia. (2017). Statistik Industri di Indonesia. Retrieved 12 1, 2017, from Kementrian Perindustrian Republik Indonesia: http://www.kemenperin.go.id/statistik/exim.php
Kerberdle, C. F. (2008). Reducing Machine Setup & Changeover Times. Learn how to gain valuable manufacturing capacity in a very short time, applying creativity and common sense before capital.
Ketkamon, K., & Teeravaraprug, J. (2009). Value and Non-value Added Analysis of Incoming Order Process. Proceedings of the International MultiConference of Engineers and Computer Scientists. II, p. 3. Hong Kong: IMECS.
Kiran, D. R. (2017). Total Quality Management: Key Concepts and Case Studies. Oxford: Elsevier Inc.
Koning, H. d., & Mast, J. d. (2006). A rational reconstruction of Six Sigma's Breakthrough Cookbook. International Journal of Quality and Reliability Management, 23(7), 766-787.
Lowry, S., Maynard, H. B., & Stegemerten, G. J. (1940). Time and Motion Study and Formulas for Wage Insentives. New York and London: McGraw Hill.
Lukas, S. (2013, October 8). Kuartal III 2017, Industri Mainan Masih Lesu. (R. Agus, Interviewer)
Lukas, S. (2018, January 2). Pengusaha Mainan Mengeluh Penjualan Menurun. (E. Nurlaela, Interviewer)
McLachlin, R. (1997). Management Initiatives and Just-in-Time Manufacturing. Journal of Operations Management, 15, 271-292.
Melton, T. (2005). THE BENEFITS OF LEAN MANUFACTURING: What Lean Thinking has to Offer the Process Industries. Chemical Engineering Research and Design, 83(A6), 662-673.
Metzinger, A., & Latif, N. (2003). Lean Manufacturing Techniques Reduce Lead Time for Implant Production. American Society for Engineering Education, 1-11.
Meyers, F. E., & Stewart, J. R. (1992). Motion and Time Study for Lean Manufacturing. (1st, Ed.) Pearson.
Mundell, M. E. (1960). Motion and Time Study: Principles and Practice (3rd ed.). Prentice Hall.
Niebel, B. W., & Freivalds, A. (1998). Methods, Standards, and Work Design (10th ed.). McGrawHill Companies.
Niebel, B., & Freivalds, A. (2009). Methods, Standards, and Work Design. (Twelveth, Ed.) McGraw-Hill.
Nyman, L. R. (1992). Making Manufacturing Cells Work. Michigan: Society of Manufacturing Engineers.
Patel, N., & Chauhan, N. (2015). Benefits of Value Stream Mapping as A Lean Tool Implementation Manufacturing Industries: A Review. International Journal for Innovative Research in Science & Technology, 1(8), 53-57.
Quality Scotland Organization. (2003). Process Mapping. Quality Scotland Foundation, p. 2.
Rother, M., & Shook, J. (1998). Learning to See: Value Stream Mapping to Add Value and Eliminate Muda (1 ed.). Cambridge: The Lean Enterprise Institute.
Schroeder, R. G., Linderman, K., Liedtke, C., & Choo, A. S. (2008). Six Sigma: Definition and underlying theory. Journals of Operations Management, 26, 536-554.
Shah, R., & Ward, P. T. (2003). Lean manufacturing: context, practice bundles, and performance. Journal of Operations Management, 21(2), 129-149.
Shah, R., & Ward, P. T. (2003). Lean Manufacturing: Context, Practice Bundles, and Performance. Journal of Operation Management, 21, 129-149.
Shah, R., & Ward, P. T. (2007). Defining and developing measures of lean production. Journals of Operation Management, 25, 785-805.
Shier, R. (2004). Statistics: Paired T-Test. Mathematics Learning Support Centre, 1-3.
Shingo, S., & Dillon, A. P. (1985). A REVOLUTION IN MANUFACTURING: THE SMED SYSTEM. Productivity Press.
Shingo, S., & Dillon, A. P. (1985). A Revolution in Manufacturing: The SMED System. Portland: Productivity Press.
Shingo, S., & Dillon, A. P. (1989). A Study of the Toyota Production System: From an Industrial Engineering Viewpoint. Tokyo: Productivity Press.
Singh, B., & Garg, S. K. (2011). Value Stream Mapping: Literature Review and Implications for Indian Industry. International Journal of Advanced Manufacturing Technology, 53(5-8), 799-809.
Surapaty, S. C. (2015, September 29). Angka Kelahiran di RI Tiap Tahun Setara Jumlah Penduduk Singapura. (I. Akuntono, Interviewer)
SYSPRO. (2014). Five Tips to Achieve a Lean Manufacturing Business. Syspro: Simplifying your success, 1-8.
Tersine, R. J., & Hummingbird, E. (1995). Lead-time reduction: the search for competitive advantage. International Journal of Operations & Production Management, 15(2), 8-18.
Tilley, D. S. (1989). VALUE-ADDED ACTIVITIES AS A RURAL DEVELOPMENT STRATEGY: DISCUSSION. Sourthern Journal of Agricultural Economics, 37-40.
Tracey, M. (1998). The Importance of Logistics Efficiency to Customer Service and Firm Performance. The International Journal of Logistics Management, 9(2), 65-81.
Woehrle, S. L., & Abou-Shady, L. (2010). Using Dynamic Value Stream Mapping and Lean Accounting Box Scores to Support Lean Implementation. Mankato: Minnesota State University.
Womack, J. P., & Jones, D. T. (1996). Lean Thinking: Banish Waste and Create Wealth in Your Corporation (1st ed.). New York: Free Press.
Womack, J. P., & Jones, D. T. (1996). Lean Thinking: Banish Waste and Create Wealth in Your Corporation (Second ed.). New York: Free Press.
- Articles published in CALYPTRA are licensed under a Creative Commons Attribution-ShareAlike 4.0 International license. You are free to copy, transform, or redistribute articles for any lawful purpose in any medium, provided you give appropriate credit to the original author(s) and the journal, link to the license, indicate if changes were made, and redistribute any derivative work under the same license.
- Copyright on articles is retained by the respective author(s), without restrictions. A non-exclusive license is granted to CALYPTRA to publish the article and identify itself as its original publisher, along with the commercial right to include the article in a hardcopy issue for sale to libraries and individuals.
- By publishing in CALYPTRA, authors grant any third party the right to use their article to the extent provided by the Creative Commons Attribution-ShareAlike 4.0 International license.