PENERAPAN LEAN MANUFACTURING UNTUK MENINGKATKAN PRODUKTIVITAS SISTEM PRODUKSI DI PT. Z
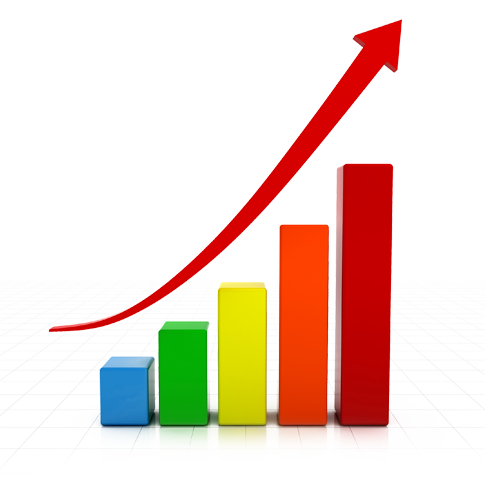

Abstract
PT. Z is a cocoa powder manufacturer that located in Sidoarjo, East Java. The factory wanted to implement the concept of Lean Manufacturing to overcome their problems such as, production loss and powder (scrap) which was spreading over their production floor and warehouse. This factory could improve their production system’s productivity with the deployment of Lean Manufacturing concept. Percentage of scraps and losses for initial condition is about 0,076% and 1,987%. Cycle time for grinding process and mixing process for initial concept is about 3,49 hours/ton and 14,2 hours/5ton. Process Cycle Efficiency (PCE) for the initial condition is 81%. After implementing the improvement initiatives, there were some differences on the indicators. Percentage of scraps and losses for the new condition was about 0,054% and 1,542%. Process Cycle Efficiency (PCE) was increased and becoming 82% with cycle time for grinding process is 2,7 hours/ton and 11,86 hours/5ton for mixing process.
Downloads
References
Bhamu, J., & Sangwan, K. S. (2014). Lean manufacturing: literature review and research issues. International Journal of Operations & Production Management, 34(7), 876-940.
Chauhan, G., & Singh, T. (2012). Measuring parameters of lean manufacturing realization. Measuring Business Excellence, 16(3), 57-71.
Cortes, H., Daaboul, J., Duigou, J. L., & Eynard, B. (2016). Strategic Lean Management: Integration of operational Performance Indicators for strategic Lean management. IFAC-PapersOnLine 49-12, 65-70.
Dennis, P. (2007). Lean Production Simplified : A Plain Language Guide to the Worlds Most Powerful Production Systems. New York: Productivity Press.
Feld, W. (2000). Lean Manufacturing : Tools, Techniques, and How to Use Them. Boca Raton, Florida: St. Lucie Press.
Gaspersz, V. (2007). Lean Six Sigma for Manufacturing and Service Industries : Strategi Dramatik Reduksi Cacat/Kesalahan, Biaya, Inventori, dan Lead Time dalam Waktu Kurang dari 6 Bulan. Jakarta: Gramedia Pustaka Utama.
Hanif, R. Y., Rukmi, H. S., & Susanty, S. (2015). Perbaikan Kualitas Produk Keraton Luxury Di PT. X dengan Menggunakan Metode Failure Mode and Effect Analysis (FMEA) dan Fault Tree Analysis (FTA). Jurnal Online Institut Teknologi Nasional, 3, 137 -147.
Hines, P., & Rich, N. (1997). The seven value stream mapping tools. International Journal of Operations & Production Management, 17(1), 46-64.
Hines, P., & Taylor, D. (2000). Going Lean. Cardiff: Lean Enterprise Research Centre.
Roszkowska, E. (2013). Rank Ordering Criteria Weighting Methods - A Comparative Overview. Optimum. Studia Ekonomiczne, 14-33.
Singh, B., Garg, S., Sharma, S., & Grewal, C. (2010). Lean implementation and its benefits to production industry. International Journal of Lean Six Sigma, 1(2), 157-168.
Wignjosoebroto, S. (1992). Teknik Tata Cara dan Pengukuran Kerja (2 ed.). Jakarta: Guna Widya.
Wignjosoebroto, S. (1993). Pengantar Teknik Industri. Jakarta: Guna Widya.
- Articles published in CALYPTRA are licensed under a Creative Commons Attribution-ShareAlike 4.0 International license. You are free to copy, transform, or redistribute articles for any lawful purpose in any medium, provided you give appropriate credit to the original author(s) and the journal, link to the license, indicate if changes were made, and redistribute any derivative work under the same license.
- Copyright on articles is retained by the respective author(s), without restrictions. A non-exclusive license is granted to CALYPTRA to publish the article and identify itself as its original publisher, along with the commercial right to include the article in a hardcopy issue for sale to libraries and individuals.
- By publishing in CALYPTRA, authors grant any third party the right to use their article to the extent provided by the Creative Commons Attribution-ShareAlike 4.0 International license.